Navigating the Future: My Journey in Industrial Automation and Robotics
- Leo Boghozian
- Jun 3, 2024
- 4 min read
Updated: Jul 15, 2024
I had the privilege of being employed at McMurray Stern, where I gained firsthand experience with Industrial Robots like FANUS, HAI, STOW, Addverb, and Schaefer robotic systems. In addition to this, I was involved in the design, production, assembly, and testing of End of Arms Tools and accessories.
One of the initial tasks I undertook was creating a camera mount for the FANUC CRX-10iA/L Collaborative Robot that would incorporate the FANUC 3DV/400 3D vision sensor. Please refer to figure 1 for details. The mount design was produced using FDM 3D Printing technology, then assembled and tested internally within a few days.

Figure 1: FANUC 3DV./400 camera and OnRobot VGC-10 Sunction Gripper integrated with the FANUC CRX robot. The camera mount and the suction cup pointer is designed and 3D Printed internally.
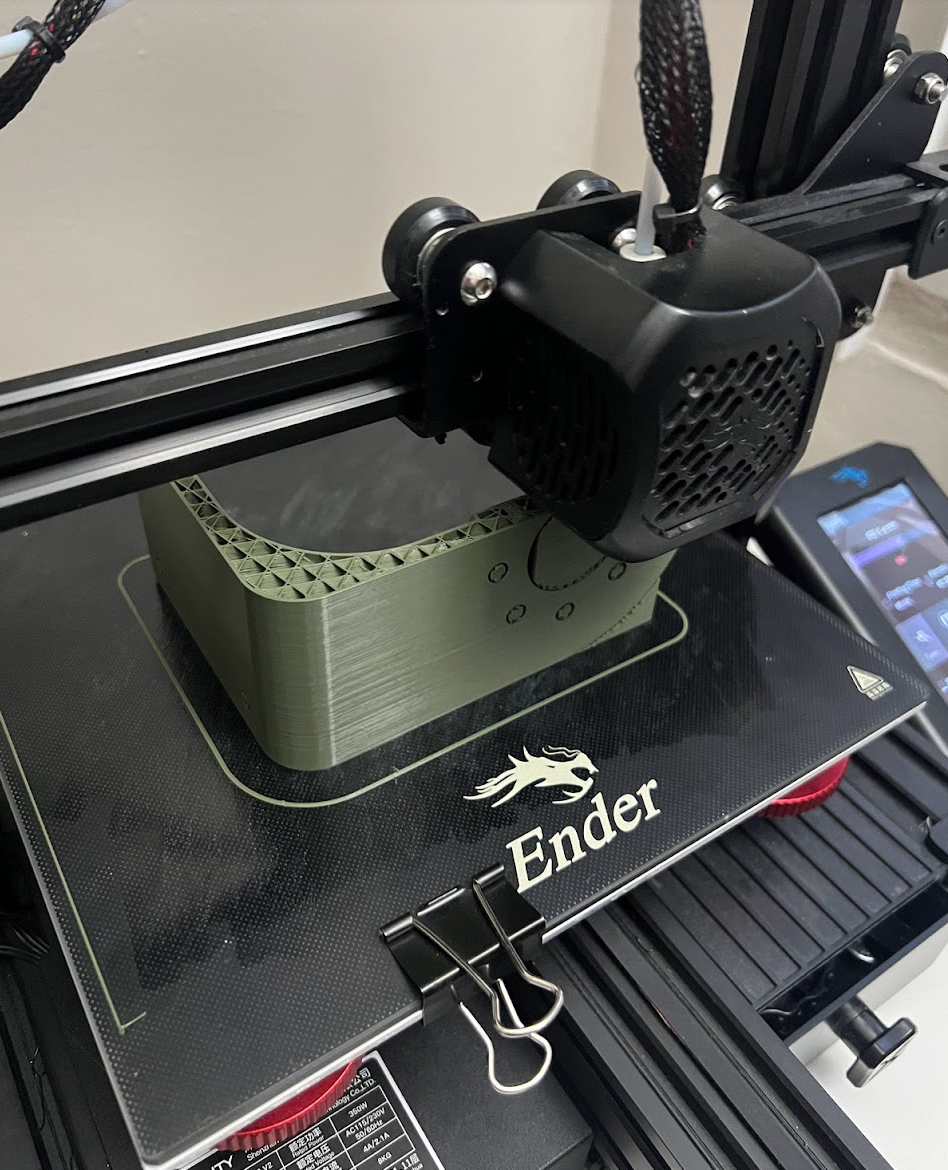
Figure 2 displays a camera mount being produced through 3D Printing with PLA+ (Polylactic Acid) material, utilizing cubic infill, a robust 3D pattern consisting of cubes positioned on a corner. This orientation effectively prevents overhangs, ensuring high strength in every direction while minimizing the undesired pollowing effect on the top layer. The cubic pattern is ideal for functional components that necessitate strength across all axes.
In figure 3 below, you can see the camera mounts 3D printed using various materials: PLA (white), PLA+ (green), and ABS (Transparent). Initially, PLA and PLA+ were used for fit testing, followed by printing the camera mount in ABS for its durability, heat resistance, and cost-effectiveness.
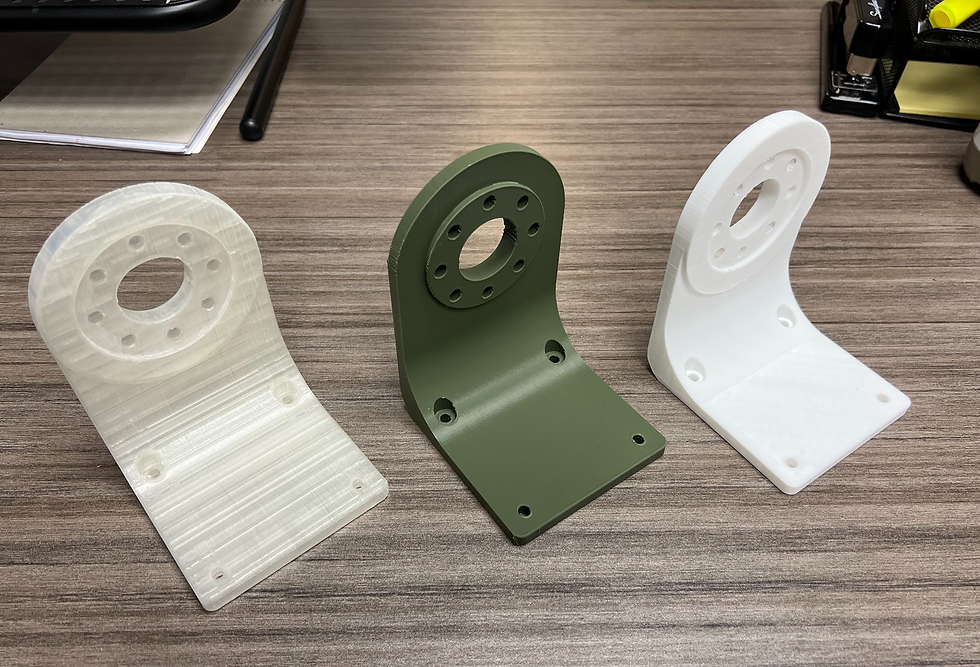
Figure 3: Camera mounts 3D Printed in different materials, such as PLA (white), PLA+ (green) and ABS (Transparent).
Subsequently, a script was developed to enable the CRX robot to pick and place objects using its 3D vision system and the OnRobot suction gripper after mastering the programming techniques. A demonstration video, labeled as video 1, showcases the robot picking chocolate from a bin and accurately placing it at a specified location.
Video 1: Demonstration video of the CRX robot picking chocolate from the bin and placing it at a designated spot.
To accomplish the identical pick & place operation using a Vertical Lift Module system, the suction gripper needed to be extended to enhance its depth range. This adjustment was necessary to prevent any collisions with the camera or nearby objects when the robot retrieves an item from a particular bin. Leveraging 3D Printing technology, I manufactured the suction gripper extender internally and attached it to the End of Arm Tool (EOAT).

Figure 4: Utilized 3D Printing technology to manufacture suction gripper extender to improve the reach of the robot.
To enable the FANUC CRX collaborative robot to work seamlessly with the Scheafer Vertical Lift Module (VLM) at increased operational speeds, I created a support base featuring square cross-sectional bars that extend outward to fit snugly within the VLM's base, figure 5. This design is akin to how a forklift pocket smoothly slots into wooden pallets. The primary function of this base is to provide stability to the robot during operation and securely position it in its designated location.

Figure 5 illustrates the FANUC CRX robot installed on a vertical riser, which is subsequently linked to a support base for seamless integration with the Schaefer VLM system.
The CRX collaborative robot is seen in action alongside the Schaefer Vertical Lift Module (VLM) to meet a particular customer order in videos 2 and 3. Using its 3D vision system, the robot locates the requested KitKat chocolate within the VLM bin. Once the item is identified, the robot approaches the target, employing the VGC-10 OnRobot suction gripper to pick up the requested item before carefully depositing it in a designated spot for the user to retrieve.
Video 2: Showcases the CRX collaborative robot in action, collaborating with the Schaefer Vertical Lift Module to complete a customer order request.
Video 3: Showcases an alternate perspective of the CRX collaborative robot in action alongside the Schaefer Vertical Lift Module to process a customer order.
Here is a video of me at the 2022 ATXWest convention, supervising the CRX robot to ensure the proper functioning of all systems, while also enabling attendees to engage, learn about the systems, and receive their preferred candy from a robot.
Video 4: Overseeing the CRX collaborative robot working with the Schaefer VLM system at the 2022 ATXWest convetion.
I was solely responsible for another design project, which involved creating a mobile putwall for the Omoron LD 250 autonomous mobile robot (AMR), as shown in figures 6 and 7. This mobile putwall was divided into 4 sections to facilitate the FANUC CRX robot in placing objects in each section to arrange the customer's order. Once the CRX robot finished its task, it would signal the Omoron AMR to move to the next location with the mobile putwall. Typically, this next location would be a specific area where workers or robots could retrieve the items from these sections to package and prepare them for shipping orders.

Figure 6: Front side of a mobile puttwall integrated with the Omoron LD 250 Autonomous Mobile Robot.

Figure 7: Rear side of a mobile puttwall integrated with the Omoron LD 250 Autonomous Mobile Robot.
Additional Activities
I also worked on interior designs for a new technology center, and proposed solutions to the CEO. Collaborated with contractors and technicians to bring the design to life.

Spotlight from the company.

Comentarios